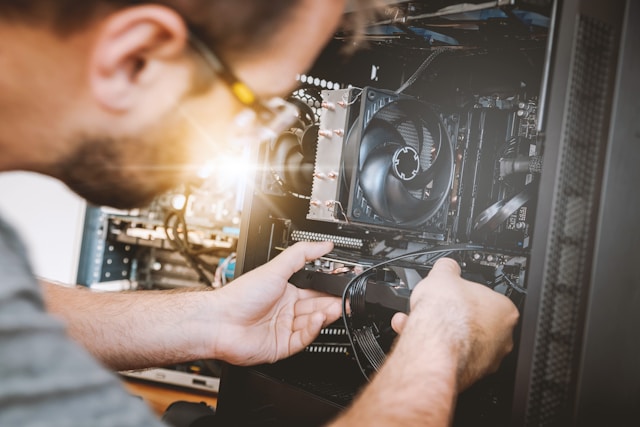
製造DX成功の鍵!システム導入の前に知っておくべき3つのポイント
「製造DXを導入したいけど、何から始めればいいの?」「DXを成功させるために気をつけるべきポイントは?」と悩んでいる製造業の経営者や担当者の方も多いのではないでしょうか。 実は、製造DXを成功に導くには、導入前に押さえておくべき3つの重要なポイントがあります。 この記事では、製造DXの概要から、導入前に知っておくべき3つのポイント、そして成功事例までを詳しく解説します。製造DXの導入を検討している方は必見の内容となっています。
ポイント1: 現状の分析と課題の特定、効果の予測
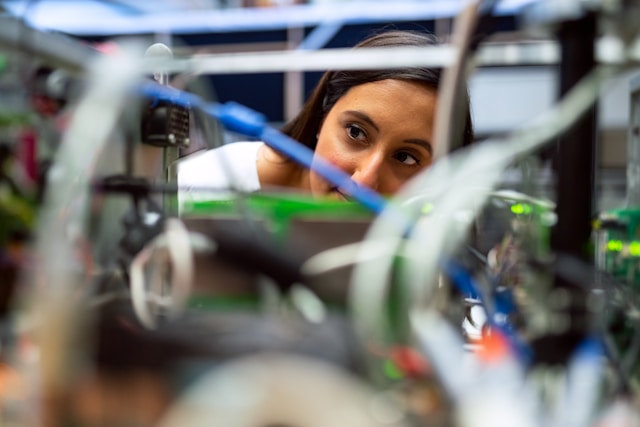
現状の分析
まずは自社の現状を正しく把握することが重要です。現在の製造プロセスや業務フローを分析し、非効率な部分や改善の余地がある領域を特定します。そのためには、ヒアリングやアンケート、ワークショップを通じて、現場が抱えている課題や要望を収集することも効果的です。
工程設計を変えたり、すぐに対策できる課題を解消して製造プロセスの合理化を十分に行った上で、残った課題に対してデジタル系ソリューションの適用可否を検討します。合理的でないプロセスを効率化しても、さほど効果は上がらない可能性が高く、DXで求められるレベルの変革は期待できません。
課題の特定
製造DXに取り組む前に、取り組むべき対象となる現場の課題を明確にすることが重要です。また、課題が膨大かつ多岐にわたる場合は、表層的な問題となっている事象のみをとらえるのではなく、「なぜ」と問いかけを数回繰り返し根本的な要因を探したり、それらに共通する構成要素を課題として見つけ出す必要があるかもしれません。
どのような課題でも、落ち着いて分析して構成要素に落とし込めば、取り組みやすくなります。また、課題が複数ある場合は、デジタル技術の適用のしやすさや、低予算での実現可能性、そして成功した際の効果の大きさなどを基準にして、優先順位をつけて個々に取り組むことが効果的です。
逆にユーザ部門の課題解決を第一の目的とせずに、IT部門などの主導で課題不在のデジタル技術の導入をはかり、DX を目指したシステム導入の実績をつくろうとするケースが見受けられます。こうした場合は、技術先行で課題を見つけるような順序での議論が進み、IT部門の予算でシステム導入が推進されるため、ユーザ部門による課題へのオーナー意識が希薄となりがちで、本質的な解決にはいたらずあまり効果が出ずに失敗に終わるケースが多いといえます。
課題にフィットするソリューションの選定
製造DXに活用できるソリューションは多岐にわたります。IoTやAI、ロボティクス、ビッグデータ解析など、様々なベンダーから多様なソリューションの選択肢が提示されています。自社の課題や目的、導入および運用体制に最も適合しており、投資対効果の高い技術を選ぶことが肝要です。
例えば、工場の自動化を進めるならロボット技術、需要予測の精度を上げるならAIと機械学習といった具合です。また、外部の委託先に実装を依頼しないのであれば、機能や性能面で選択するよりも、ユーザがみずからシステム導入できるような使いやすいパッケージソリューションを選択することが勧められます。段階的な導入を想定して、拡張性も考慮する場合は、スケーラビリティの高い技術を選ぶことで、事業の成長に合わせてシステムを柔軟に拡張できます。
投資対効果(ROI)の算出
経営層の承認を得るためには、投資対効果(ROI)の提示が必要です。目標とされる経済的な効果を算出して、それに実用なデジタル化の投資との比較を行い、予算の獲得を正当化します。
ところが、効果の予測と数値化が難しい課題も存在します。例えば、まずは生産工程の可視化を行わないと、今後取り組むべき課題を特定できないが、可視化だけでは導入効果が数値化できないため、予算を得ることが難しいという状況などがあげられます。たしかに可視化することが目的と伝えると効果が不明確で、投資回収のイメージがわきません。
ここでは、妥当性の高い仮説をたてることが重要になります。たとえば、システム導入でリモートでの可視化ができると、その効果により現場にいかなくても生産工程の状況がリアルタイムで把握できようになります。それによって、働き方が変わり少人数での経営が可能になるという仮説をたて、その効果を経済的な価値に置き換えて経営層に伝え、その仮説が妥当とみなされれば予算が認められる可能性は高くなるでしょう。
先進企業では、財務的な評価に加えて、従業員満足度による離職率の低減や技能伝承による事業継続などの効果も含めた総合的な評価方法を確立している企業もあるとのことです。
ポイント2: リーダーシップの醸成と体制の構築
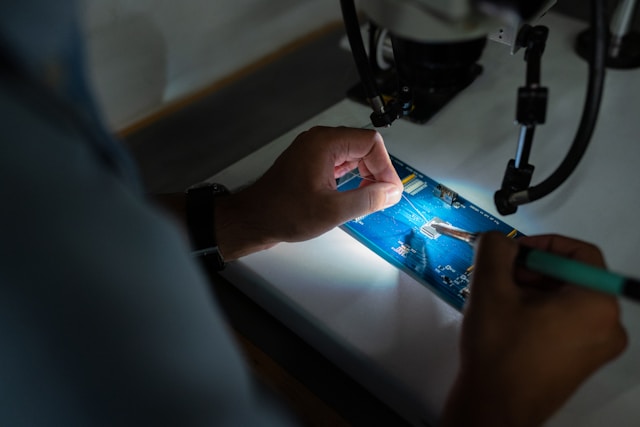
リーダーシップの醸成と組織文化の変革
製造DXを成功に導くには、単に新しい技術を導入するだけではなく、プロジェクトに参加するメンバーの強いリーダーシップが不可欠です。個々の参加メンバーがリーダーシップを発揮して積極的にDXの推進ができる環境をつくることが重要です。また、試行錯誤はつきものですので、失敗を許容する組織文化の変革も重要といえます。
DXを成功に導くには意識改革が必要となる場合もあります。「今のやり方で十分」「新しいシステムは使いこなせない」という現場の抵抗感も、DX推進の大きな障壁となる場合があります。現場の従業員がDXの意義を理解し、前向きに変化を受け入れる姿勢になってもらうためには、システム導入のメリットを丁寧に説明して理解を得ることが大切です。
例えば、作業の自動化によって単純作業から解放されデジタル化により削減できた時間を、いままで取り組む時間が確保できなかった工程改善や業務効率化など、より創造的な業務にあてることができます。また技能向上や研修などの取り組みに充てられることを明確に示すことで、前向きに受け入れてもらいます。現場メンバーの積極的な参加を促し、知見を取り入れながらDXを進めることで、当事者意識を高め、自発的な改善提案を引き出すことができます。
経営層からのサポートの獲得
DXを進めるには、上位の管理職のスポンサーシップが必要です。経営層がDXの意義を理解し、強いコミットメントを示すことで、全社的な取り組みを推進しやすくなります。トップ自らがDXのビジョンを示し、変革の必要性を社内に浸透させることが求められます。また、DXの実行には、部門間の壁を越えた連携が不可欠です。上位の管理職がリーダーシップを発揮し、部門間の調整役を果たすことで、スムーズな協働体制を構築できます。
現場のリーダーシップと経営層のスポンサーシップの連携が成功の鍵となります。経営層は経営課題を共有して、明確なビジョンと投資判断を示し、現場は経営課題の解決につながる実践的な対策やアイデアを共有することで実効性の高い施策を打ち出せます。経営層とのコミュニケーションの不足が生じれば、「コストがかかりすぎる」「効果が見えにくい」という懸念につながり、十分な支持が得られないケースが散見されます。
関係者を巻き込む推進体制の構築
IoT導入を成功に導くためには、適切な推進体制の構築が不可欠です。重要なことは、キーパーソンを早期から巻き込むことです。最低限、以下の役割を明確にする必要があります:
- プロジェクトオーナー:IoTプロジェクトへの投資判断を行います。
- 推進リーダー:IoTシステムを企画・提案してプロジェクトを推進します。
- 現場リーダー:現場の課題やユーザの意見を集約してチーム内で共有します。
上記リーダーを中心に参加メンバーをそろえて体制を整え、導入プロジェクトを推進することになります。特定領域の課題やIoTの技術に関しては、それらの知見を持ったベンダーなど社外の人員による支援を一時的にうける必要があることも想定されます。
プロジェクトの規模と必要性に応じて、経営層、営業部門、製造部門、技術部門、人事部門などの代表者で構成されるプロジェクトチームを設置します。このチームが中心となって、導入計画の立案から実行、効果検証までを組織間の利害関係を調整しながら一貫して管理します。
製造部門に閉じることなく、営業・マーケティング部門も巻き込み、市場のニーズを取り込むことによって、製造部門としてどのような貢献ができるか考えることでブレークスルーが生まれる可能性もあります。DXとともに発生するメンバーのリスキリング(再訓練)については人事部門の協力が得られるかもしれません。
業務委託先との連携
製造DXの実行には、様々な専門知識やノウハウが必要とされます。特に、デジタル技術に関する知見やリソースが社内に不足している場合、外部の業務委託先と連携することが有効です。単に指示された通りのものを開発するシステムインテグレータでよいのか、製造現場の知見を持ち、業務改善の提案ができるコンサルティング力のあるベンダーにするのか、また、自社との文化的な相性や、長期的なサポート体制も考慮すべきポイントです。
委託先との連携では、役割分担や責任範囲を明確にすることが重要です。自社と委託先、それぞれの強みを生かした協働体制を構築することで、DXをスムーズに進められます。
ポイント3: 段階的な導入と維持コストの確保
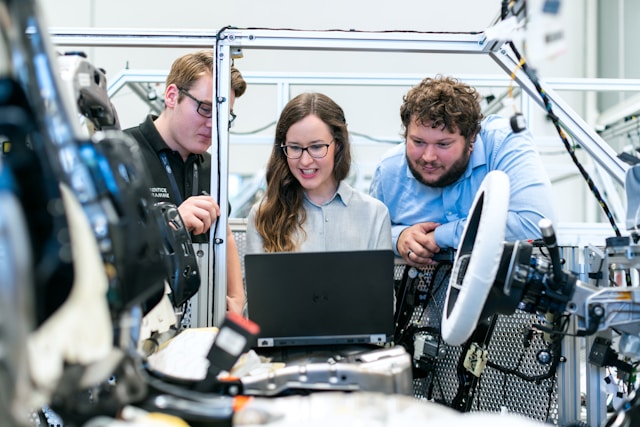
実証実験(PoC)と段階的な導入
実証実験(PoC)は、本格導入に向けた重要なステップです。成功のポイントは、評価する技術や適用範囲、試用期間を適切に設定することにあります。たとえば、特定の製造ラインや工程に限定して、IoTセンサーの設置やデータ収集システムの導入を試験的に行います。実験期間は3〜6ヶ月程度に設定し、明確なKPIを定めて効果測定を行うことなどが推奨されます。
実証実験で効果が確認できたら、段階的な展開を進めていきます。この際、重要なのは「スモールスタート」の原則です。たとえば、最初は1つの製造ラインでの導入から始め、成果を確認しながら他のラインへと展開していきます。各段階で得られた知見や課題を文書化し、展開時のノウハウとして蓄積することで、効率的な水平展開が可能になります。
段階的な目標の設定
段階的な導入計画とともに、効果目標を設定します。目標は具体的で測定可能なものにすることが重要です。例えば、「生産性を20%向上させる」や「リードタイムを3日短縮する」といった具合です。また、目標達成によってもたらされるビジネスインパクトも併せて示すことで、DX導入の意義を社内で共有しやすくなります。
工場の自動化プロジェクトのように、最初から100%をめざさなければ価値がはっきりしないテーマもありますが、そうでない場合は一般的に、段階的な導入ごと中間目標を複数設定して、当初は60%や70%程度の効果を目指し、徐々に完成形に近づけることで無理なく効果をあげていくような導入を進めることが推奨されます。
効果測定の仕組み化
DX導入の効果を継続的に測定し、可視化することは、プロジェクトの持続的な推進に不可欠です。効果測定では、定量的指標(生産性、不良率、リードタイム等)と定性的指標(従業員満足度、技能習熟度等)の両面からの評価が重要です。
実践的な仕組みとして、週次での KPI レビューと月次での施策の見直しを組み合わせることで、PDCAサイクルを確実に回すことができます。特に重要なのは、現場作業者自身が効果を実感できる指標の設定です。
運用・維持コストの確保
運用維持には意外にコストを要します。実証試験の結果を確認したり、プロジェクトの早い段階で、継続的に発生するコストがまかなえるだけの効果が出ていることを確認してから投資すべきかどうかの判断を行います。相当の効果がでていないと維持コストが見合わないため、定着せずに終了するケースも見受けられます。
また、初期導入コストと導入後の維持コストの原資が異なる場合も注意が必要です。たとえば、初期導入コストはIT部門が負担しても、システム納品後の運用維持はユーザ部門で予算を負担するような取り決めだったりすると、中長期の維持コストの確保が難しくなるケースもあります。
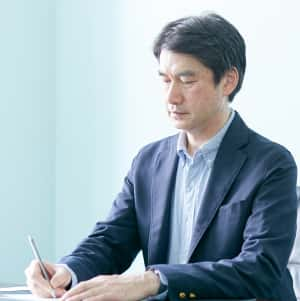
お気軽にお問い合わせください。
工場経営の課題を解決するDX戦略の策定とIoTシステム導入を支援します。