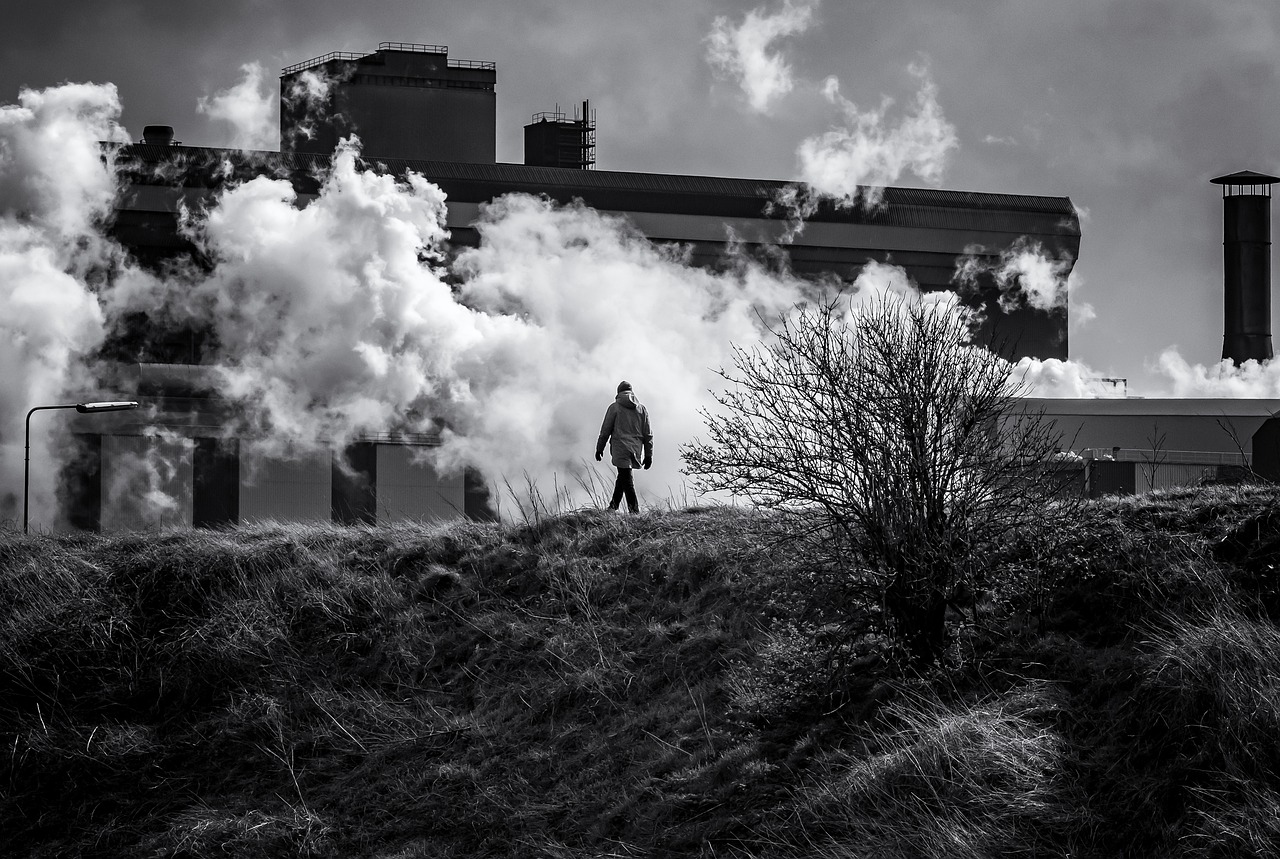
工場IoTの導入効果|製造現場における導入メリットと投資対効果
「工場IoTって導入効果がありそうだけど、実測値がイメージできない…」「投資回収できるのか不安…」「現場への導入をどう説得すればいいのだろう?」と悩んでいる工場長や製造部門の責任者の方も多いのではないでしょうか。
実は、工場IoTの導入効果は、稼働率向上、歩留まり改善、直行率など、明確な数値で把握することができ、適切な導入計画があれば1-2年での投資回収も十分可能なのです。この記事では、工場IoT導入による実践的な効果とともに、投資対効果の算出方法を解説していきます。
製造現場の課題とIoT導入の必要性
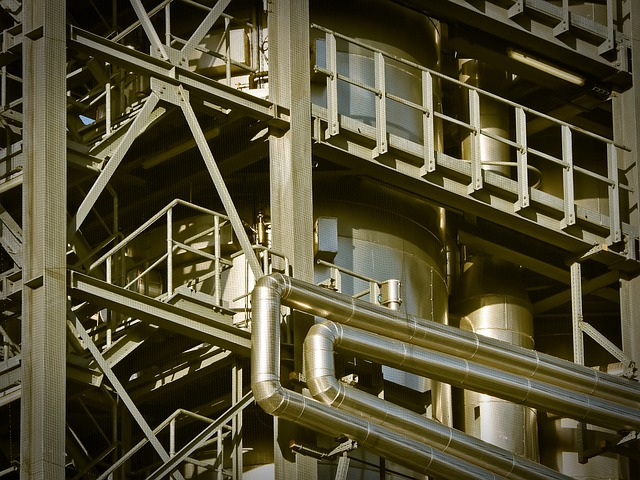
製造業を取り巻く環境は、国内労働人口の減少や国際競争の激化により、かつてないほど厳しい状況に直面しています。そんな中で注目を集めているのが工場IoTです。工場IoTとは、製造現場の設備や機器をネットワークでつなぎ、データを収集・分析することで、生産性向上を目指す取り組みをさします。
製造現場が直面する重要課題
日本国内の製造業は、就労人口の減少や、設備の老朽化、グローバルサプライチェーンの再編、不安定な通貨価値などの影響によって、様々な問題に直面しています。主な課題として以下のようなものがあげられています。
属人化された工程と人手不足への対応
深刻化する人手不足は、製造現場における最重要課題となっています。ベテラン社員の高齢化や若手人材の確保難により、技能伝承が困難になっているだけでなく、日々の生産活動にも支障をきたすケースが増えています。作業の属人化も深刻な問題です。ベテラン社員の経験に依存していては、不在の際、効率的な生産を維持することが難しくなり、品質も不安定になります。
不安定な原材料コストと生産性向上への要求
原材料の仕入れコストは上がる一方であるにもかかわらず、コスト増加をそのまま価格に転嫁できないため、さらに効率的な製造によるコスト削減が求められています。設備の老朽化に伴う保全業務の増加も、現場の負担を大きく増やしています。予期せぬ故障による生産ラインの停止は、納期遅延や品質問題につながるリスクとなっています。
環境問題へ意識の高まりと規制への対応
環境負荷の少ない製造プロセスで生産された製品を求める購買行動が求められ、サステナビリティが企業価値のひとつとして認められるようになりました。実際に、製造時に要したエネルギー消費量を炭酸ガス排出量に換算して報告する義務など、特に欧州を中心にして環境規制が強化されつつあります。
工場IoTによる課題解決への期待
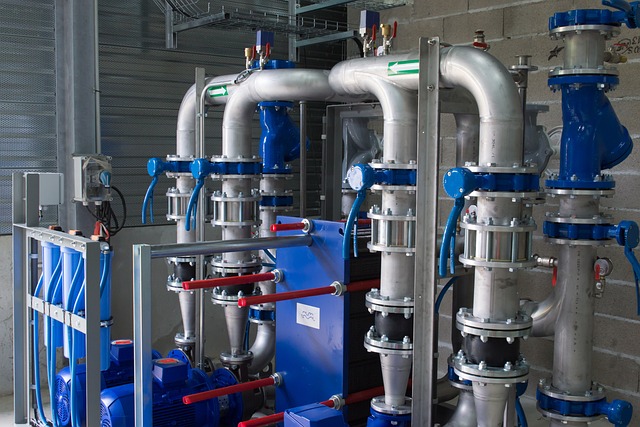
自動計測されたデータの収集と可視化
工場IoTでは、製造設備や製造環境に取り付けたセンサーが、稼働状況や環境データをリアルタイムに収集します。温度、振動、電流値といった様々なデータを24時間365日モニタリングすることで、人手では把握できなかった製造現場の状況を可視化します。
従来、現場の隅々まで足を運び、目視や手作業による計測で行われていた管理から、ネットワーク化されたセンサーとデータを活用した管理への移行が進められています。どのような場所からでも、瞬時に設備の稼働状況を把握することができるとともに、品質のばらつきや設備の異常を早期に発見することが可能になります。
AIによるデータ分析と最適化
自動計測、収集されたデータは、一元的に管理され分析が行われます。例えば、データ分析によって設備の稼働状況を監視したり、環境負荷を低減する施策を立案したりすることが可能になります。つまり、経験や勘に頼らない、データに基づいた製造現場での意思決定が可能となるのです。
また、データ分析を行うことで製造ノウハウのデジタル化を行うことも可能となります。いままで暗黙知として共有化が難しかった熟練作業者の動作や、経験による判断を数値化することができるようになります。データやAIが生成した機械学習のモデルとして形式知化することで、組織内で共有することが可能となり技能伝承の効率化が期待されています。
工場IoT導入により期待される効果
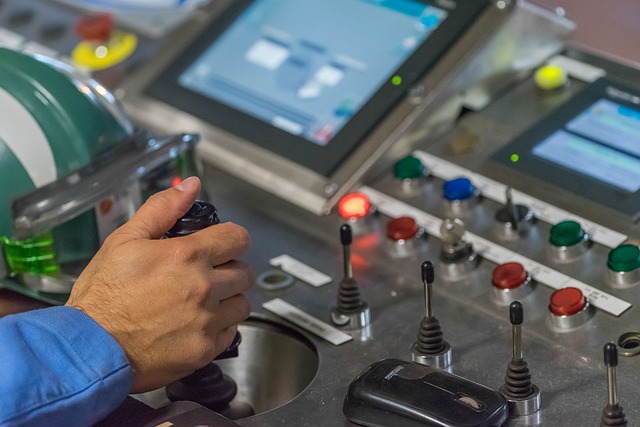
IoTを工場に導入することで、様々な領域での生産性の向上に貢献して、幅広い効果が期待できます。ここでは、その一部を紹介していきます。
少人数での工場経営
IoTによる記録・報告業務の自動化やリモート管理によって、効率的な管理体制が構築でき、少人数での工場経営の実現に貢献します。
自動管理による効率化
実績情報の管理における作業効率の向上は、工場IoT導入による最も分かりやすい効果です。データ収集の自動化により、これまで手作業で行っていた日報作成や生産実績の記録作業が大幅に削減されます。ある自動車部品製造業では、作業記録のデジタル化により事務作業時間が従来比60%削減され、その時間を品質の向上活動に充てることで生産性が30%向上したと報告されています。
リアルタイムな生産状況の把握
IoTシステムが提供するリアルタイムな可視化は、リモートでの製造現場の状況把握を可能にします。現地へ移動しなくてもPCやモバイル端末から各工程の稼働状況や生産量を監視できるとともに、常時監視しなくても、トラブル発生時には能動的にアラートを発報、発生箇所がピンポイントで通知されます。このような効果により、少人数でのオペレーションが可能となります。
エネルギー使用量の計測とコストの削減
IoT導入によるデータ分析により、様々なコスト削減効果が期待できます。また、製品や部品ごとに生産に要したエネルギー消費量(カーボンフットプリント)の計算ができるようになります。
エネルギーコストの削減
各生産設備に通信機能付きの電力量計を取り付け、ネットワーク化して設備ごとの電力消費量をリアルタイムで計測します。細かくエネルギー計測を行うことで、いつどの設備でエネルギー消費が増えるのか、その傾向を分析することで平準化できないか検討します。また、アイドル状態で待機電源のみ使用している設備を発見して主電源をおとしたり、必要な場所だけ空調や照明が使われるよう自動制御することもできます。
カーボンフットプリントの算出
各生産設備に取り付けられた通信機能付きの電力量計をネットワーク化して、工程情報と関連付けを行うことによって、工程ごとの部品や製品の製造に使用したエネルギー消費量を把握することができます。部品や製品の個体ごとに通過してきた工程でのエネルギー消費量の総和を計算することで、各個体の製造に要したエネルギー消費量の算出が可能となります。
品質管理の高度化とトレーサビリティの実現
IoTによって収集された詳細なデータを分析することで、高度な品質管理が可能となります。
品質管理の高度化
製造工程の各データを統合的に管理することで、品質に影響を与える要因を特定しやすくなります。温度、湿度、加工条件などの変動要因と品質の相関関係を分析することで、最適な製造条件を導き出せます。食品製造業の事例では、製造環境のモニタリングと製造レシピの最適化により、不良率が5%から1%未満に減少した例もあるようです。
トレーサビリティの実現
手書きや手入力での記録を廃止して、センサーによる計測値をネットワークで収集して自動で記録するシステムを導入します。このデータを製造履歴と関連付けて記録しておけば、万が一の品質問題発生時も、トレーサビリティにより原因の特定と対策が迅速に行えるようになります。また検査データの改ざんなどの不正行為を防ぐことにもIoTは貢献します。
IoT導入の投資対効果の算出
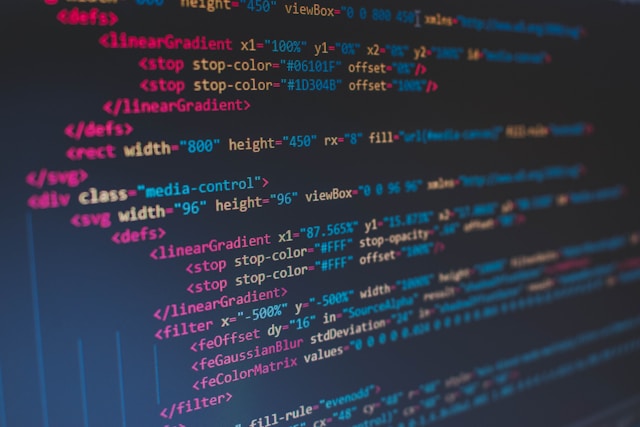
経営者や工場長にとって、IoT導入の投資対効果は最大の関心事です。実際の導入においては、初期投資と維持コストの適正な見積りと現実的な効果予測が重要になります。
投資対効果の算出方法
工場IoTの投資対効果の算出は、IoTシステム構築・維持を行うために十分な投資を得るために不可欠な作業です。一般的な経営指標である、投資対効果(ROI : Return On Investment )が用いられることが多く見受けられます。これは投資によって得られる利益を投資額で割り、100を掛けて算出します(ROI = 利益÷投資額×100)。
取り組む課題によっては、単純に生産工程でのコスト削減などにとどまらず、効果的な営業活動や製品価値を向上させることによって顧客満足度に影響を与えることもありうるため、複数の部門での効果も数値化して、投資対効果の算出に加える必要がでてきます。
一般的な投資規模と回収期間
中規模の加工・組立タイプの製造プロセスにおいて、一般的な初期投資額は以下のような内訳となります:
- センサー・ネットワーク機器:数万円から数十万円程度
- システム構築:数十万円から数百万円程度
- 導入支援:数百万円から数千万円程度
- 教育研修:数万円から数百万円程度
実際にはIoT を適用したい製造プロセスの特性や解決すべき課題、求められている効果の規模によって、多様な種類や台数の機器が選択され、それらを組み合わせることでシステムが構成されるため、上記金額については、かなり幅のある記載となっています。これらの投資に対し、多くの製造業では2-3年での投資回収を目標としています。
一般的な導入効果の指標
製造現場におけるIoT導入の効果はケースバイケースといえますが、一般的には以下のような効果を期待されるケースが多く見受けられます:
- 設備稼働率:平均して15-20%向上
- 生産リードタイム:20-25%短縮
- 品質不良率:30-40%削減
- エネルギーコスト:10-15%削減
これらの効果は、継続的な運用により、さらなる向上が期待されます。
実際には IoT を適用したい製造プロセスの特性や解決すべき課題によって、求められている効果の規模は異なってきます。つまり、母数となる改善対象の規模が十分大きければ、仮にたった1%程度の改善効果でも十分に投資が回収できるケースもあります。逆に規模が小さければ50%を超える割合の改善効果でも投資が回収できないことになるケースもあります。
仮に、毎月1億円のコストが発生している製造プロセスで、1%のコスト削減が実現すれば毎月100万円のコスト削減が可能となり、年間で1,200万円の経済価値を提供していることになります。
投資効果の評価では、定量的な指標だけでなく、従業員の技術力向上や、リアルタイムな意思決定能力の強化など、長期的な競争力への影響も考慮する必要があります。これは、「デジタル時代の工場経営」という大きな文脈の中で捉えるべき投資判断なのです。
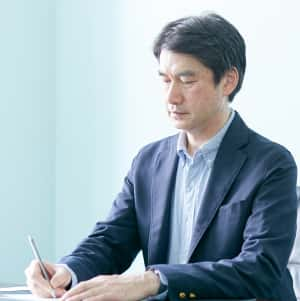
お気軽にお問い合わせください。
工場経営の課題を解決するDX戦略の策定とIoTシステム導入を支援します。