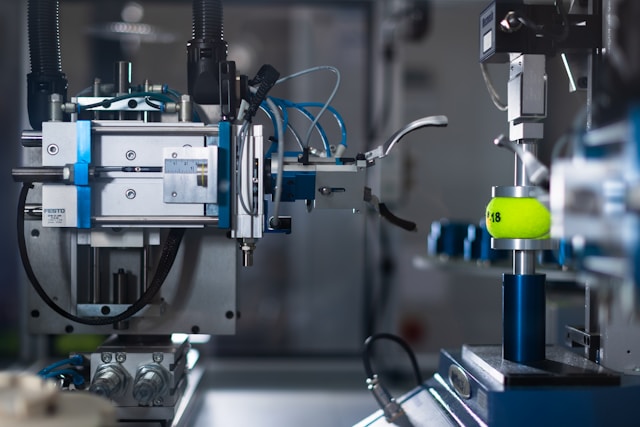
製造DXのメリットと導入効果|〜2025年最新!製造DXのトレンド予測〜
製造DXとは、製造プロセスにおけるデジタルトランスフォーメーション(DX)を指します。それは、デジタル技術を活用して、効率化や自動化を図ることで、生産性の向上やコスト削減を実現することを目的としています。
「製造のDXって本当に効果があるの?」「投資対効果が見えづらくて、経営層を説得できない…」「実践的な成功事例が知りたい」と悩んでいる方も多いのではないでしょうか。
この記事では、製造DXのメリットと実際の導入事例について解説します。経営層への提案に使える成功例など、検討に必要な情報をお伝えしていきます。
製造DXとは
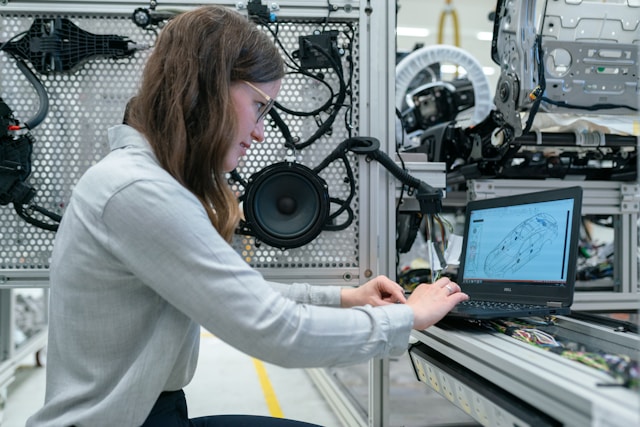
製造業におけるデジタルトランスフォーメーション(DX)
製造業におけるデジタルトランスフォーメーション(DX)は様々な領域で展開されています。インターネット通信機能を持つインテリジェントな製品をベースに、新たなユーザ体験を創造するスマート・コネクティッド・プロダクト、製品設計や開発のための業務や出荷後のサービス業務の効率化などに貢献するデジタルツイン、またデータ分析によって需要予測の精度を上げたり在庫・物流の最適化を行うサプライチェーンの領域など、製造企業のあらゆる領域でデジタルトランスフォーメーション(DX)つまりデジタル技術による変革がおきることが期待されています。
製造DXとその目的
製造業における様々なDXへの取り組みのなかでも、特に製品や部品を生産する工場でのDXについては、製造DXあるいは工場DXと呼ばれるデジタル技術の適用領域を構成しています。デジタル技術によって製造プロセスの効率化や自動化を図ることで、いままでとは異なるレベルで大幅に生産性を向上させ、工場経営に変革をもたらすことを目指しています。
製造DXの取り組みには、IoTやAI、ロボティクスなどの先進テクノロジーの導入が含まれます。なかでも工場領域でのIoTとデータ分析は大きな投資を必要とせず、比較的簡単に取り組むことができ、早く効果を出すことが期待できます。デジタル化によって、いままでカン・コツにたよっていた業務でのヒト依存の暗黙知が、客観的なデータとしてヒトに依存しない形式知となります。つまり事象を細かくデジタルデータとしてとらえて、それを分析することで、以前はなんとなくヒトの感覚で認識していた工場内での出来事をデータとして分析可能な状態にすることができます。
製造DXが目指しているのは、単なる製造現場のデジタル化ではなく、デジタル技術を活用して製造プロセス全体を革新する取り組みです。それは製造業が直面している様々な課題を解決し、競争力を高めるための戦略的な取り組みでもあります。例えば、少子高齢化による労働力不足への対応や、グローバル市場での競争力強化、環境規制への対応などが挙げられます。製造DXは、これらの課題にデジタル技術で立ち向かい、新たな価値を創出することを目指しているのです。
製造DXが注目される理由
製造DXが注目を集めている理由は大きく分けて2つあります。
1つ目は、デジタル技術の急速な発展です。オープンな標準通信プロトコルを搭載したり、通信機能が強化されたPLCなどの制御機器の普及によって、それらを組み込んだ生産設備のネットワーク化とデータの収集が以前よりも容易になりました。またスマートホンやタブレットなどの消費者製品として開発された端末機器が工場でも使用されるようになり、リアルタイムで生産ラインを監視制御することが廉価かつ簡単に実現できるようになってきています。
2つ目は、製造業を取り巻く環境の変化です。グローバル競争の激化や顧客ニーズの多様化によって、製造業には高い生産性と柔軟性が求められるようになりました。また、熟練工の高齢化と労働人口の減少による人手不足も深刻な問題となっています。これらの課題に対応するために、製造DXによる業務の効率化と自動化が不可欠だと考えられているのです。
製造DXのメリットと効果
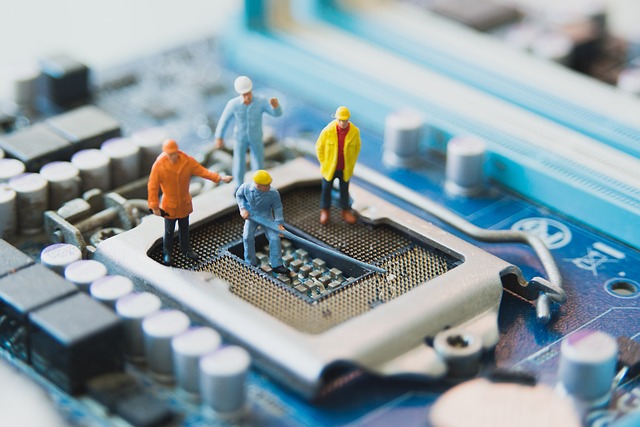
製造DXを実現した企業は生産性を大幅に向上させる可能性があります。主に以下のような効果が実現されています。
データドリブンな工場経営
製造DXの最大のメリットは、経営判断のデジタル化です。リアルタイムでの生産状況把握や、データに基づく的確な意思決定が可能になります。これにより、生産現場での変化への迅速な対応や、正しい既存設備の能力判定と新規設備への投資判断が可能となります。
従来の経験と勘に頼った管理から、リアルタイムデータに基づく管理への転換により、生産性の向上、コストの削減、市場への迅速な対応など、多方面にわたるメリットをもたらします。データ活用に成功した企業では、データ分析による製造プロセスの最適化、ダウンタイムの削減や原材料のロス低減によって、生産性が平均30%向上したという報告もあります。
検査工程の自動化と品質の安定
検査工程に産業用カメラを設置して、マシンビジョンシステムによる検査の自動化が実現されています。以前は、これら自動検査システムの設定には専門知識が必要で、導入後も定期的な調整に手間がかかっていましたが、現在はAIによる画像分析により最小限の専門知識での設定や調整が可能になっています。目視にたよっていた検査作業が自動化できるだけではなく、ヒューマンエラーによる不適合品の流出を90%以上削減できることが実証されています。
また、単に合否判定を正確にして不適合品流出を削減するだけでなく、合否判定の基準となる数値データを記録することによる効果も期待されています。たとえば製造プロセスの各工程で収集されたデータと合否判定の基準となる数値データの関連付けをして分析することで、不適合が発生する要因を特定して、不良品の発生を未然に防ぎ製品品質の安定化を目指す試みが行われています。
自動化と効率化
自動化によって検査工程に限らず、単調な作業や重労働からの解放を実現し、従業員の労働環境を大きく改善します。データ活用による業務の効率化で、残業時間の削減や休暇取得率の向上にもつながります。これは人材採用や定着率の向上にも好影響を与えています。
紙の伝票からコンピュータシステムによる管理にすることで、特に生産計画の自動立案と工程間連携の最適化により、大幅な効率化が実現可能です。紙の伝票を廃止して受注から出荷までのプロセスをすべて自動化することによって、従来2週間要していた生産リードタイムを平均して5日にまで短縮した事例も報告されています。
生産性向上を実現した製造DX成功事例
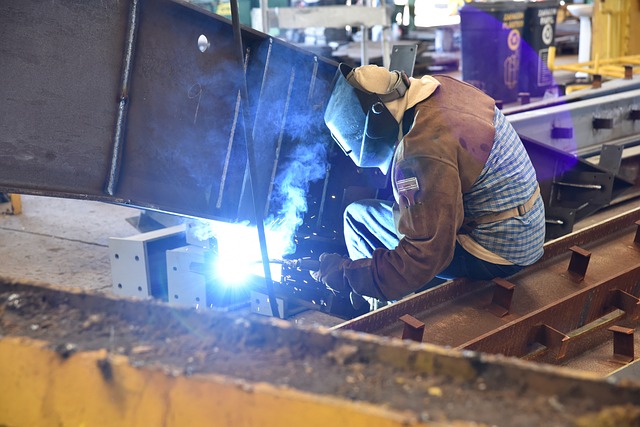
大手製造業A社の生産管理改革事例
導入前の課題と施策内容
A社は従業員1000名規模の自動車部品メーカーで、人手不足と技能伝承の課題に直面していました。生産現場では熟練作業者の経験と勘に依存する部分が多く、品質のばらつきや生産性の停滞が経営課題となっていました。
この課題に対し、まず製造ラインにIoTセンサーを設置し、設備稼働データと作業者の動作データの収集を開始しました。収集したデータは生産管理システムと連携させ、リアルタイムでの進捗管理を可能にしました。さらに、熟練作業者のノウハウを数値化し、標準作業手順としてデジタル化することで、技能伝承の仕組みを構築しました。
中小製造業B社の段階的導入事例
限られた予算での推進方法
従業員150名の精密機器メーカーB社は、初期投資を3,000万円に抑えた段階的なDX導入を実施しました。まず、生産現場の課題分析から着手し、最も効果が見込める検査工程のデジタル化に焦点を絞りました。
実践的な取り組みとして、まず品質検査工程にAI画像認識システムを導入し、検査員の作業負荷を軽減。その後、得られた効果を基に経営層の承認を得ながら、工程間の連携システムや生産計画の最適化システムへと段階的に展開していきました。
達成した効果と成功要因
B社はシステム導入当初から生産性を向上させることに成功しました。特筆すべきは、検査工程での不良流出がゼロになったことで、顧客からの信頼度が大幅に向上し、新規受注の増加にもつながった点です。成功の最大の要因は、「小さく始めて大きく育てる」という段階的なアプローチと、現場社員と共に進めた業務最適化の取り組みを継続したことにあります。
現場作業者からは「以前は検査作業に追われて工夫を重ねる時間が取れなかったが、システム導入後は本来の技術開発に時間を使えるようになった」という声が上がっています。
2025年最新!製造DXの課題と将来展望
注目の最新技術トレンド
従来の機械学習による製造プロセスの異常検知や品質予測、コンディション・ベースド・メンテナンス(CBM)による予兆保全などから、デジタル技術の適用範囲は今後も徐々に広がっていくことが予想されています。特に予兆保全については、より廉価なソリューションによって、対象となるアセット(設備資産)が広がることが期待されます。
また、パッケージソフトの活用に加えて、ローコード・ノーコードツールが進化することにより、現場主導でのデジタル化も加速することが期待されています。これらのツールが活用できれば、ITスキルが十分ではない担当者でも、IT部門や業務委託先に頼らず、迅速なシステム導入ができるようになります。
新たなトレンドとして製造領域での生成AIの活用が注目されています。たとえば工場内で過去に発生したトラブルへの対策に関する記録を参考に、当該トラブル未経験の担当者へ迅速に適切なアドバイスを行ったり、適切な大規模言語モデル(LLM)と検索拡張生成(RAG)を設定するなど環境を整えることで、生成AIが効果を発揮することが期待されています。
今後5年間で、製造業のDXはさらに加速することが予想されます。特に、欧州での規制に起因する細かなエネルギー使用量の計測への対応や、サプライチェーンの管理対象が工場内部のプロセスへと拡大していくなど、新たな課題への対応も求められています。各企業が自社の状況に応じた適切なDX戦略を策定し着実に実行していくことが、製造業を成功させる可能性を持つ要因として、これまで以上に重要となっています。
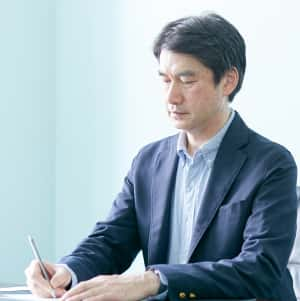
お気軽にお問い合わせください。
工場経営の課題を解決するDX戦略の策定とIoTシステム導入を支援します。